When it comes to excellent inventory management, it’s important to continuously strike the right balance between supply and demand, to avoid overstocking and understocking. To help inform your ordering practices, you can turn to a simple yet powerful technique called ABC analysis.
ABC analysis allows you to prioritize stock based on value and demand, using a simple method that categorizes inventory into three groups. While there are different ways to calculate ABC analysis and put it to work in your organization, supply chain management software like StockIQ helps you do it easily, quickly, and accurately.
In this guide, we’ll walk you through everything you need to know about ABC analysis, and how you can use StockIQ to help with this process.
What is ABC Analysis?
In most businesses, not all inventory is created equal. What exactly does this mean? Instead of all SKUs being equally valuable to your business, you probably have some items that are more important to your company and some that are less important. These items are the ones that generate the most revenue, while your least important items are the ones that generate the least amount of revenue.
ABC analysis (also called ABC stratification), is rooted in the principle that roughly 80% of a company’s revenue often comes from just 20% of its inventory. By focusing on these most valuable items, businesses can optimize their inventory decisions, improve efficiency, and best serve their customers.
Understanding the ABC Categories
ABC analysis divides inventory into three categories:
- A Items (high value, low quantity)
These are the most critical inventory items. They account for a small percentage of your total stock, but a large portion of total value. Due to their importance, they require the tightest inventory control, careful demand forecasting, accurate monitoring, and frequent reordering.
- B Items (moderate value, moderate quantity)
These items fall in the middle, contributing moderately to total value, and making up a reasonable portion of stock. They require a balanced approach to inventory and require a medium amount of inventory control.
- C Items (low value, high quantity)
These items make up the majority of stock but contribute the least to overall value. They require minimal oversight and simpler replenishment strategies, such as bulk ordering and less frequent stock checks.
By classifying inventory into these categories, businesses can focus their resources where they matter most: improving stock management, reducing waste, and enhancing overall profitability.
StockIQ Note: There’s one caveat to remember regarding ABC analysis. You might have customers who come to you to buy items in your A category, but who also equally value items in your B or C category. This might mean that running out of items in the B or C category (or running low on stock) could cause these customers to churn, even though they’re primarily coming to you for your A-based items.
Benefits of Using ABC Analysis
There are many practical benefits to using ABC analysis for inventory management in your business.
1. Improved inventory control
By categorizing inventory based on value, businesses can allocate resources more effectively. High-value items in the A category receive the most attention (ensuring they’re always in stock). In contrast, low-value items in the C category require minimal monitoring (reducing time and effort spent on this less-critical inventory).
2. Cost savings and better cash flow
ABC analysis helps businesses optimize inventory purchasing decisions, reducing excess stock and associated costs (such as storage costs and obsolescence). Studies show that oversupply leads to $163 billion in wasted inventory every year. By prioritizing high-value items, companies can invest in their inventory wisely, leading to better cash flow management.
3. Reduced stockouts and overstocking
By focusing on the most important inventory items, businesses can maintain appropriate stock levels, preventing shortages that lead to lost sales. At the same time, controlling C items properly prevents overstocking of slow-moving items.
4. Increased operational efficiency
Since ABC analysis streamlines inventory management, businesses can spend less time and resources on unnecessary stock checks, and more time on strategic decisions. This can improve warehouse organization, faster order fulfillment, and better overall productivity.
5. Enhanced customer satisfaction
Ensuring that your most important items are always available leads to faster, more consistent order fulfillment, and fewer stockouts. This can improve both the customer experience and brand reputation. Keep in mind that data shows when companies focus on the customer experience, they can significantly boost revenue.
ABC Analysis Best Practices
To properly leverage ABC analysis in your business, here are some best practices to keep in mind:
- Define clear classification criteria: Set specific percentage thresholds for your categories. Consider not just consumption value, but additional factors like turnover rate and lead time.
- Regularly review and update classifications: Demand, costs, and consumer buying habits change over time, so be sure to review your ABC analysis regularly (such as quarterly or annually). Reclassify inventory items as their value and demand patterns shift.
- Integrate ABC analysis with other inventory techniques: ABC analysis complements other inventory management techniques, such as Just-in-Time ordering practices. You can also implement safety stock calculations to prevent stockouts for your critical items.
- Leverage technology for better inventory insights: Modern supply chain technology (such as StockIQ) can help you automate ABC analysis. You can also use this software to track real-time stock movements and to generate demand forecasts to inform and refine inventory strategies.
StockIQ and ABC Analysis
If you’re using StockIQ as your inventory management solution, you’ll enjoy certain features that help you with the ABC analysis process. For example, ABC classes are assigned by StockIQ automatically, based on the refresh frequency that you configure in the Class Settings Groups page. ABC classes are generally based on volume-type measures, such as hits, COGS, sales, margin, etc.
To offer you a higher degree of inventory control, StockIQ also assigns additional classes:
- X Class: This special class is used for items that have essentially no movement, no usage, and are pretty much deadstock. A 50% service level is assigned to X-class items when using StockIQ’s built-in service level management. Items that come from the ERP with an inactive order policy. “Do Not Order”, “Obsolete”, “Replaced” and items will a similar policy will also be automatically assigned to the “X” class.
- N Class: A second special class, “N,” is used for new items, according to the threshold set in the Inventory Limits page. You can specify a target service level for new items, to give them a chance to succeed or fail while new, before they are subject to normal classing criteria.
StockIQ and Seamless ABC Analysis
ABC analysis is a straightforward inventory management technique that can vastly improve the way you approach ordering stock. By using advanced software like StockIQ, you can easily understand which items in your inventory fall into the A, B, and C categories, and use the right strategy for each category.
If you’re ready to deploy StockIQ in your business, let’s talk. StockIQ is a user-friendly supply chain planning suite, designed to help you boost operational efficiency, improve forecast accuracy, and simplify your strategic planning. Our tools give you a clear, accurate view of your inventory and expected consumer habits, so you can optimize ordering.
Interested in seeing how StockIQ can enhance how your business approaches inventory management? Contact us today or request a StockIQ demo.
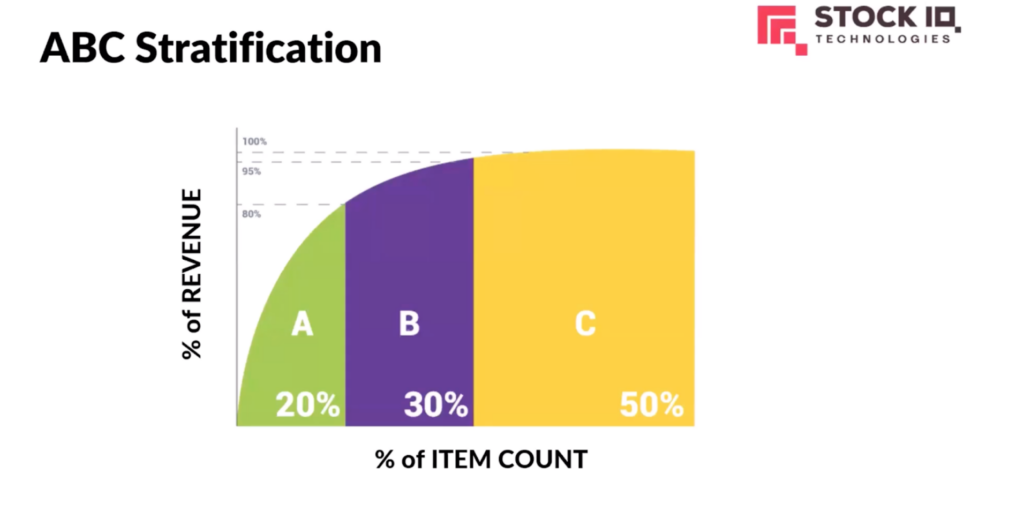