Resources
Dive in and discover how easy supply chain management can be.
Need help with supply chain management? You're in the right place. Our supply chain resources are here to help guide you every step of the way.
Articles on supply chain management
Want to learn how to cut down on stockouts and improve service? Our team of experts shares all you need to know –– from reducing inventory levels to planning ahead, so you can take control of your supply chain — the easy way.
Guides, videos, and tools for supply chain success
Take control of your supply chain today with StockIQ tutorials that cover it all — from keeping track of goods to planning how they move. Whether you're starting out or looking to get better, we've got a breakdown just for you.
Statistical Forecasting with Jeff and Jeffrey
Jeff Woodmansee and Jeffrey Porter at StockIQ will review Statistical Forecasting.
Goals of Forecasting
Jeffrey Porter and Jeff Woodmansee at StockIQ share their insights into the Goal of Forecasting.
Enhance Your Supply Chain with Free StockIQ Downloads
Unlock powerful tools to streamline your supply chain—download StockIQ's free resources today! Get immediate access to guides, templates, and insights designed to optimize your operations. Download now and start enhancing your supply chain strategy for free!
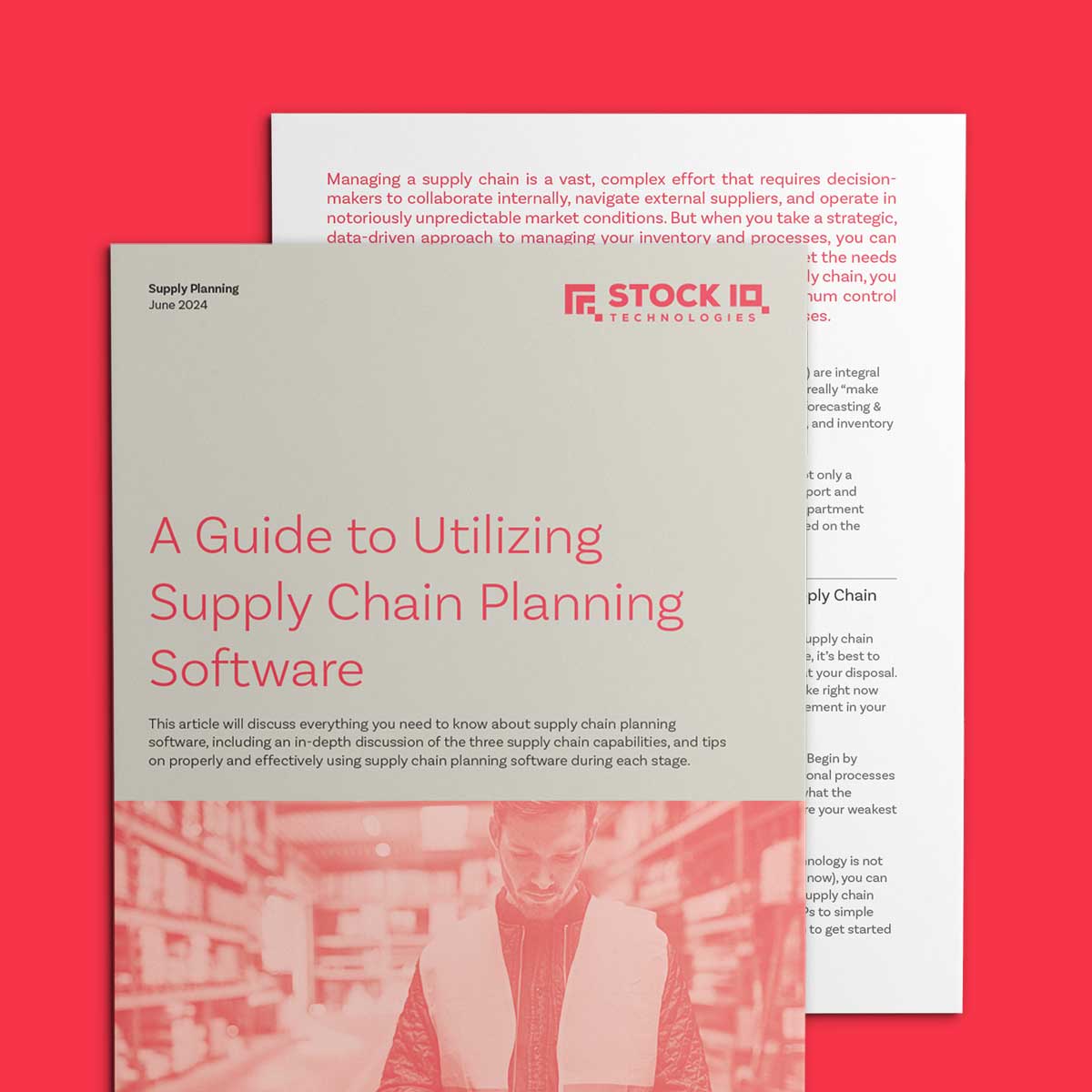
A Guide to Utilizing Supply Chain Planning Software
This article will discuss everything you need to know about supply chain planning software.
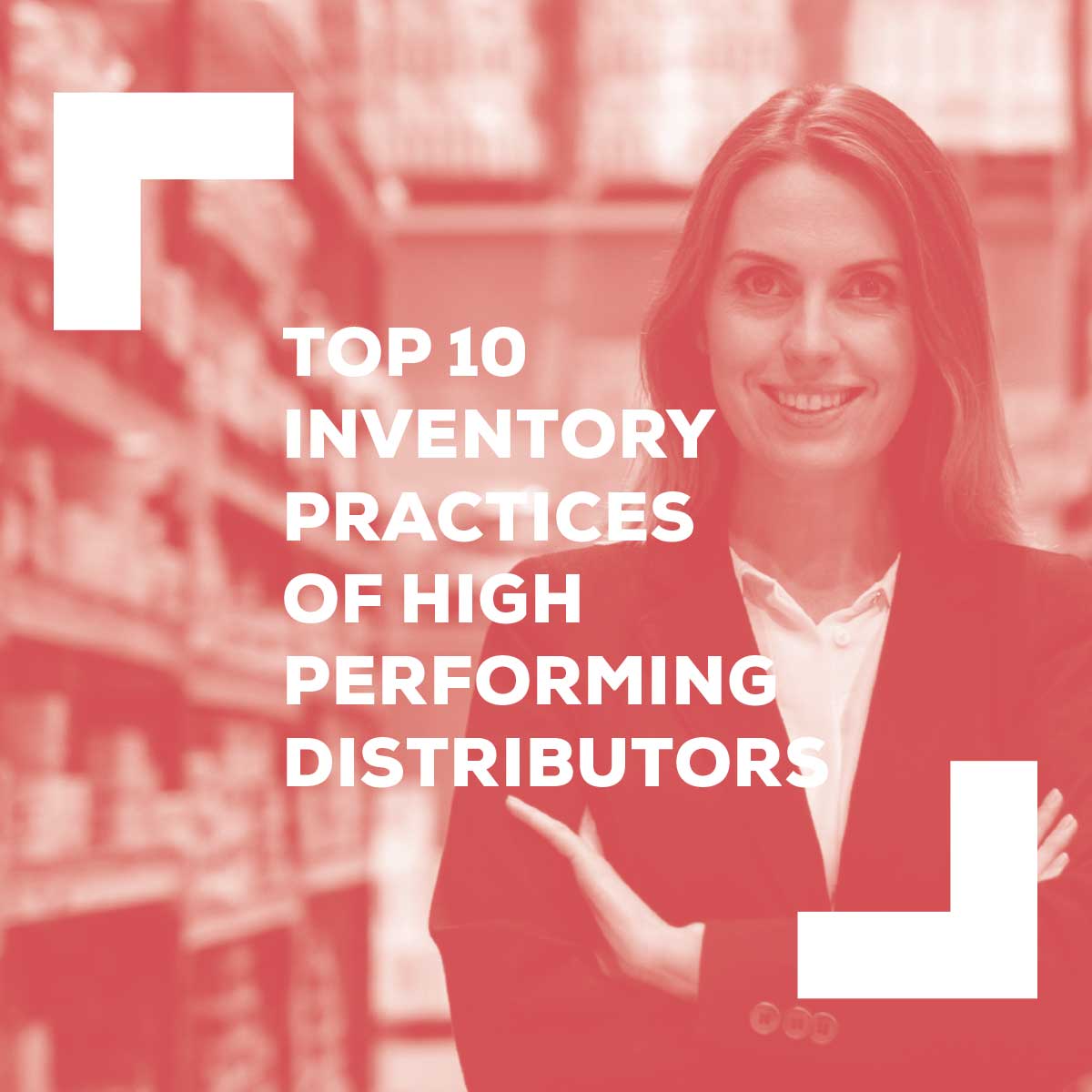
Top 10 Inventory Practices of High Performing Distributors
Inventory is the lifeblood for distributors and maintaining the right inventory on the right items at the right locations is of utmost importance for maintaining high levels of customer service and loyalty.
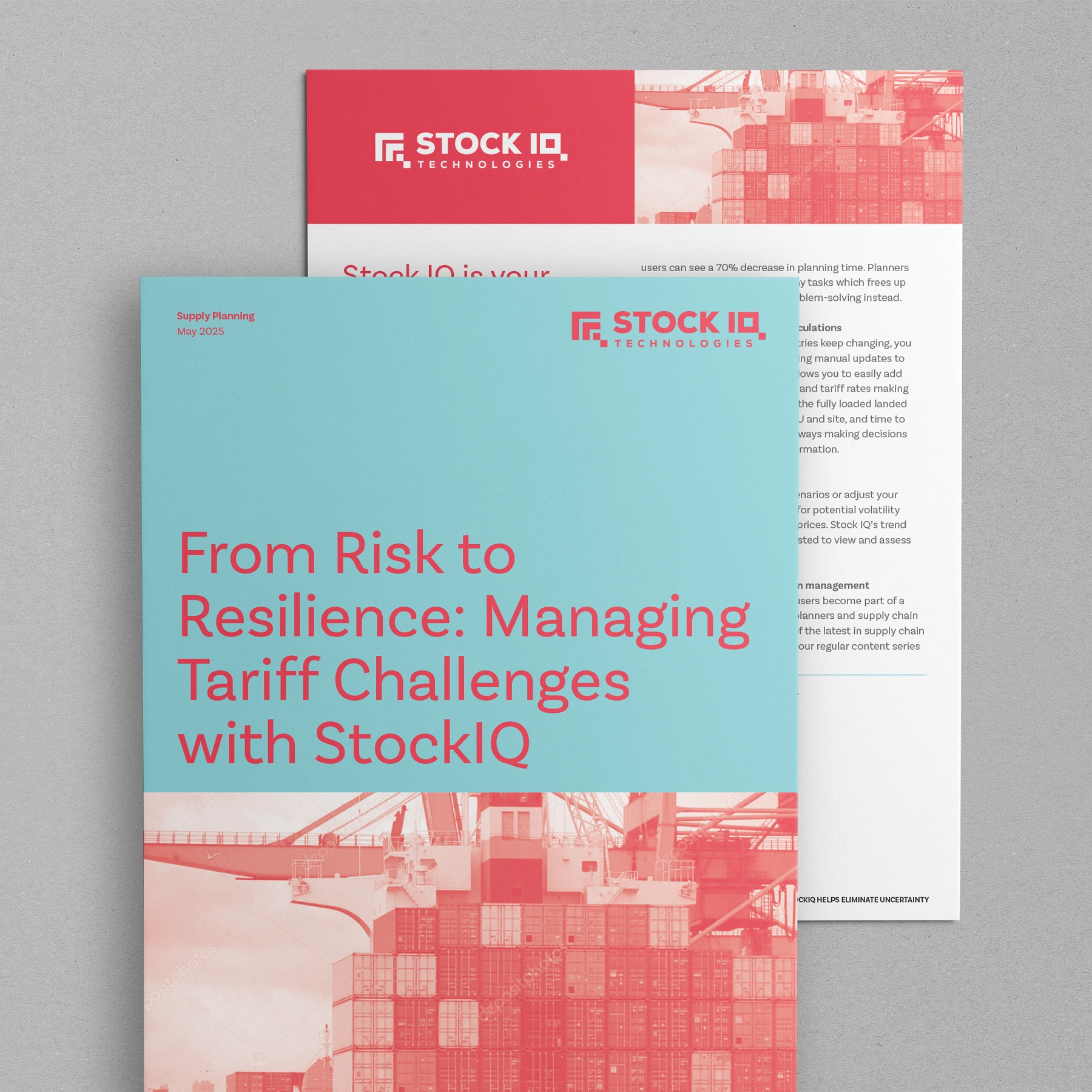